Supplying the new ozone generators in the second sterilization
station in Aleppo. As well supervising the installation
and testing. 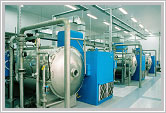
For General Co. For Hydro-projects
When adding only chlorine for sterilizing
drinking water it combines with organic and inorganic
elements exist in water, such as leaves, a family
of chemicals called trihalomethanes, or THMs, is formed,
which is a carcinogenic material.
Studies on this material show that it
cause rectal cancer and colon cancer. For this, Universal
laboratories in charge of human health care has searched
for another additional sterilizing method to get rid
of this carcinogen materials. As a result they found
that using ozone for sterilization at the first stage
then adding chlorine at the end is the best way for
sterilization, because Ozone has the following properties: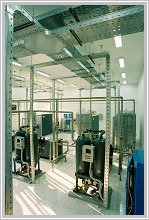
 Destroying
toxic residuals, resulted from the chlorine combination
with the materials existed in water.
 Oxygen
Saturation
 Disinfection
(bacteria and germs)
 Inactivation
of viruses.
 Fungicide
 Reduction
of fetor
 Reduction
of taste
 Elimination
of fecal bacteria
 Elimination
of Sulphur
 Oxidation
and flocculation of Mn and Fe
 Oxidation
of detergents
The station consists of three lines
to generate ozone gas, each of 10kg/h for the sterilization
of water, more than 250000 m3/h, after being treated
in the open sand filters. Each line consists of:
Air compressor – initial refrigerant –
dryer – ozone gas generator with all its accessories
of sensors, valves, filters and electrical panels
– Automation panels for monitoring, control
and operating according to the current standards in
this field – residual ozone gas destructor which
takes the floating ozone on the water surface in the
contact tanks and change it into oxygen, and drive
it out.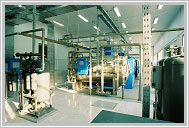
- The air compressor is to draw air
from the outside atmosphere to extract oxygen from
it. This air is pushed at 13 bar pressure, and then
received by an air collecting tank supported by filters,
required for the purification of air inside the tank,
then to get it out. There is an electromagnetic valve
to get rid of the condensation which takes place in
the tank.
- Then the air goes to the initial refrigerant, which
makes a preliminary cooling of air by a Freon compressor,
to get rid of the air humidity and to decrease the
temperature. At this stage the air is extracted from
the impurities through the filters exist on the inlet
and the outlet of the initial refrigerant.
- The air goes out of the initial refrigerant with
some humidity, which could not be got rid of. This
problem is treated inside the initial dryer that works
on freeing air completely from humidity. The dryer
consists of two bottles with aluminum silicates inside,
used in extracting the air humidity. the purpose of
existing two bottles is that when one of them operates,
the other will be in the renewing and standby phase,
so they exchange working every 10 minutes or more,
and that is according to design of the dryer. 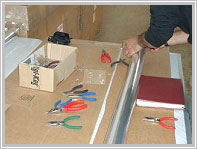
Then the air passes to the ozone generator, completely
free from humidity. The generator consists of stainless
steel body, and stainless steel pipes inside, where
the ozone generating elements are installed. The elements
are dielectrics of glass tubes, made of mixtures of
400 materials, to get high quality tubes, which are
painted from inside with a conductive material. Each
generator could contain 380 glass tubes from the both
sides, and the tubes of each side are connected to
the medium voltage net (4-8 KV), and that is to generate
an electrical arc, which makes an ionization of the
oxygen spread in the empty space formed between the
stainless steel pipes and the glass tubes, and so
O2 is changed to become O3 which is named as ozone
gas.
The working method of the station:
All of it is automated with the most up-to-date international
techniques:
 The
compressor is controlled by the microprocessor with
a screen, made by the manufacturing company of the
compressor- inside it there are all the required protections
for the drawn air and for the compressor equipment
of motor, compressor and electromagnetic valves. 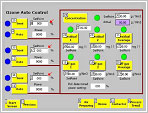
 The
initial refrigerant is controlled by a microprocessor
with a screen, made by the manufacturing company of
the refrigerator.
 The
dryer also is controlled by a microprocessor
 All
those microprocessors are connected by the central
monitoring
 panel,
which monitors the operation of the equipment continuously.
 Each
generator is controlled by PLC for commanding monitoring
and measuring with reading screens of the recent situation.
The PLC is connected with the central monitoring panel,
where we see through its screens all the information
about the station.
 The
automation process is supported by the required sensors;
the ozone leakage in the station hall is the most
important, so that orders will be given according
to the seriousness of the spread amount of the leaked
ozone, whether to decrease the generator capacity
or to stop it completely. Above that all, there are
destructors for the residual ozone which floats on
the water surface of the contact tanks, where inside
it the ozone is mixed with water. The destructors
take the residual ozone, destruct it and change it
to oxygen then throw it to the outside air. those
destructors are also connected to the central monitoring
panel and this means that:
 The
whole station is controlled and monitored by the most
up-to-date techniques and programming; and all that
is to generate the ozone, with the required amount
and time and with the less economic cost for investment,
that is what we mean by the electrical bills
|